How To Compute Cost Per Unit
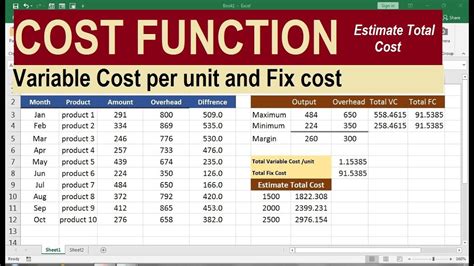
Calculating the cost per unit is a fundamental aspect of business and finance, allowing companies to determine the profitability and efficiency of their operations. This metric is crucial for making informed decisions, optimizing production, and setting competitive pricing strategies. In this comprehensive guide, we will delve into the world of cost per unit calculations, exploring various methods, real-world applications, and the significance of this concept in today's business landscape.
Understanding Cost Per Unit

Cost per unit is a measure of the average cost associated with producing a single unit of a product or service. It is calculated by dividing the total costs incurred during a specific period by the total number of units produced or provided during that same period. This metric provides valuable insights into the financial viability of a business and helps identify areas for cost optimization.
Let's consider an example to illustrate the concept. Imagine a bakery that produces and sells various types of bread. The bakery's total costs for a month include ingredients, labor, rent, utilities, and other overhead expenses. During that same month, the bakery produced and sold 5,000 loaves of bread. By dividing the total costs by the number of loaves sold, we can determine the cost per unit for each loaf of bread.
Formula for Cost Per Unit
The basic formula for calculating cost per unit is straightforward:
Total Costs | Cost Per Unit |
---|---|
Total Costs / Number of Units | Total Costs / Number of Units |

Here's a step-by-step breakdown of the calculation:
- Identify the Total Costs incurred during the period of interest.
- Determine the Number of Units produced or sold during the same period.
- Divide the Total Costs by the Number of Units to obtain the Cost Per Unit.
By applying this formula, businesses can gain a clear understanding of the average cost associated with each unit of their product or service. However, it's important to note that the calculation becomes more nuanced when considering different types of costs and the varying complexity of production processes.
Types of Costs and Their Impact

When calculating cost per unit, it’s crucial to differentiate between the various types of costs that contribute to the overall production process. Understanding these cost components is essential for accurate and meaningful analysis.
Direct Costs
Direct costs are those that can be directly attributed to the production of a specific unit. These costs typically include raw materials, labor directly involved in production, and any other expenses directly related to the manufacturing process. Direct costs are often the most variable and are influenced by factors such as production volume, efficiency, and the specific inputs required for each unit.
For instance, in our bakery example, direct costs would encompass the ingredients used in bread production, such as flour, yeast, and sugar. Labor costs for the bakers who mix, shape, and bake the bread would also fall under direct costs. These expenses are directly tied to the production of each loaf of bread.
Indirect Costs
Indirect costs, also known as overhead costs, are those that cannot be easily traced to a specific unit of production. These costs are often shared across multiple products or services and include items like rent, utilities, insurance, administrative expenses, and general management costs. Indirect costs are essential for running the business but are not directly tied to the production of a single unit.
Continuing with our bakery example, indirect costs would include the rent for the bakery premises, electricity for lighting and oven use, insurance for the business, and the salaries of administrative staff. These expenses contribute to the overall operational costs but are not directly attributable to the production of a single loaf of bread.
Variable and Fixed Costs
Another crucial distinction in cost analysis is between variable and fixed costs. Variable costs are those that fluctuate directly with the level of production. As production increases, variable costs tend to rise, and vice versa. Examples of variable costs include raw materials, direct labor, and certain utilities like electricity for production equipment.
Fixed costs, on the other hand, remain relatively constant regardless of the production volume. These costs include items like rent, insurance premiums, and salaries for permanent staff. Fixed costs are typically independent of the production output and are necessary for maintaining the business infrastructure.
Methods for Calculating Cost Per Unit
There are several methods for computing cost per unit, each suited to different types of businesses and production processes. Let’s explore some of the most common approaches.
Standard Costing
Standard costing is a widely used method that involves setting predetermined costs for various components of production. These standard costs are based on historical data, industry benchmarks, and management estimates. By comparing actual costs to standard costs, businesses can identify variances and make informed decisions to improve efficiency.
Standard costing is particularly useful for businesses with relatively stable production processes and predictable cost structures. It allows for easy identification of areas where costs deviate from expectations, enabling timely corrective actions.
Activity-Based Costing (ABC)
Activity-based costing is a more sophisticated approach that allocates costs based on the activities involved in the production process. Unlike standard costing, ABC considers the causal relationship between activities and costs, ensuring a more accurate allocation of overhead expenses to individual units.
ABC is valuable for businesses with complex production processes or those offering a diverse range of products. By identifying the specific activities and their associated costs, businesses can better understand the true cost structure of each unit and make informed pricing and strategic decisions.
Process Costing
Process costing is commonly used in industries where the production process is continuous and homogeneous, such as in the manufacturing of chemicals or textiles. This method assigns costs to units based on the average cost incurred during the entire production process.
Process costing is useful when the output of the production process is indistinguishable, and the focus is on the overall cost of the entire process rather than the cost of individual units. It provides a streamlined approach to cost allocation, making it suitable for industries with high-volume, low-variety production.
Real-World Applications
The concept of cost per unit has far-reaching applications across various industries and business functions. Let’s explore some practical examples of how this metric is utilized in the real world.
Manufacturing and Production
In manufacturing industries, calculating cost per unit is essential for optimizing production processes and ensuring profitability. By analyzing the costs associated with each unit, manufacturers can identify areas for cost reduction, improve efficiency, and make strategic decisions to enhance their competitive advantage.
For instance, a car manufacturing company can use cost per unit calculations to assess the profitability of different vehicle models. By comparing the costs of producing each model, the company can identify which models are more cost-effective and make adjustments to their production strategies accordingly.
Retail and E-commerce
Retailers, both traditional and online, rely on cost per unit calculations to set competitive prices and ensure profitable operations. By understanding the cost structure of their products, retailers can determine the minimum selling price required to cover costs and generate a profit.
Consider an online fashion retailer that sources clothing from various suppliers. By calculating the cost per unit for each garment, the retailer can set appropriate retail prices, taking into account factors like supplier costs, shipping expenses, and desired profit margins. This ensures that the retailer remains competitive while maintaining profitability.
Service Industries
Cost per unit calculations are not limited to tangible products; they are equally applicable to service-based industries. Service providers, such as consulting firms, law practices, or accounting firms, use this metric to determine the cost of delivering their services and set appropriate billing rates.
For example, a consulting firm can calculate the cost per unit of providing consulting services to a client. This calculation takes into account factors like the consultant's hourly rate, overhead expenses, and the time required to complete the project. By understanding the cost per unit, the firm can set fees that cover costs and generate a reasonable profit.
Significance of Cost Per Unit

The significance of cost per unit calculations extends beyond financial analysis. This metric has a profound impact on various aspects of business operations and strategic decision-making.
Profitability Analysis
Cost per unit calculations are a fundamental tool for assessing the profitability of a business. By comparing the cost per unit to the selling price, businesses can determine their profit margin and evaluate the financial viability of their operations. This analysis helps identify products or services that are generating the most profit and those that may require adjustments to become more profitable.
Pricing Strategies
Understanding the cost per unit is crucial for setting effective pricing strategies. Businesses can use this information to determine the minimum price required to cover costs and generate a profit. Additionally, by analyzing the cost structure, businesses can identify opportunities to differentiate their products or services through value-added features or premium offerings, allowing them to command higher prices.
Cost Optimization
Cost per unit calculations provide a clear framework for identifying areas where costs can be reduced or optimized. By breaking down the cost structure into direct and indirect costs, variable and fixed costs, businesses can pinpoint specific areas for improvement. This may involve negotiating better supplier contracts, improving production efficiency, or reallocating resources to more cost-effective areas.
Performance Evaluation
Cost per unit is a valuable metric for evaluating the performance of different business units, departments, or even individual employees. By comparing the cost per unit across various segments of the organization, management can identify high-performing areas and those that may require additional support or strategic interventions.
Future Implications and Challenges
As businesses continue to evolve and adapt to changing market dynamics, the concept of cost per unit will remain a critical tool for financial analysis and strategic decision-making. However, several future implications and challenges should be considered.
Changing Cost Structures
The cost structures of businesses are subject to change over time due to factors such as technological advancements, shifts in consumer preferences, and global economic trends. As a result, businesses must regularly review and update their cost per unit calculations to ensure they remain accurate and reflective of the current market conditions.
Sustainability and Environmental Considerations
In today’s environmentally conscious world, businesses are increasingly focusing on sustainable practices and reducing their environmental impact. As such, cost per unit calculations should incorporate sustainability factors, such as the cost of recycling, waste management, and carbon footprint reduction initiatives. By considering these factors, businesses can make more informed decisions that align with their sustainability goals.
Data Analytics and Technology
The advent of advanced data analytics and technology has revolutionized the way businesses calculate and analyze cost per unit. With the use of sophisticated software and tools, businesses can automate the collection and analysis of cost data, leading to more accurate and timely insights. Additionally, technology enables businesses to integrate cost data with other critical metrics, providing a holistic view of their operations.
Competitive Landscape
The competitive landscape of industries is constantly evolving, with new players entering the market and established businesses adapting to changing consumer demands. As a result, businesses must continuously monitor their cost per unit relative to competitors to maintain their market position and ensure their products or services remain competitively priced.
How often should businesses review their cost per unit calculations?
+Businesses should review their cost per unit calculations periodically, ideally on a quarterly or annual basis. This ensures that the calculations remain up-to-date and reflect any changes in cost structures or market conditions. Regular reviews allow businesses to identify trends, make necessary adjustments, and stay ahead of the competition.
What are some common challenges in calculating cost per unit accurately?
+Some challenges in accurately calculating cost per unit include the complexity of production processes, difficulty in allocating overhead costs, and the need for accurate and timely data. Additionally, businesses may face challenges in differentiating between direct and indirect costs, especially in industries with diverse product lines or complex supply chains.
How can businesses use cost per unit calculations to improve their pricing strategies?
+Cost per unit calculations provide valuable insights into the profitability of different products or services. By analyzing the cost structure, businesses can set pricing strategies that align with their desired profit margins. Additionally, understanding the cost per unit allows businesses to identify opportunities for value-added features or premium offerings, enabling them to command higher prices while maintaining profitability.