Finding Unit Cost
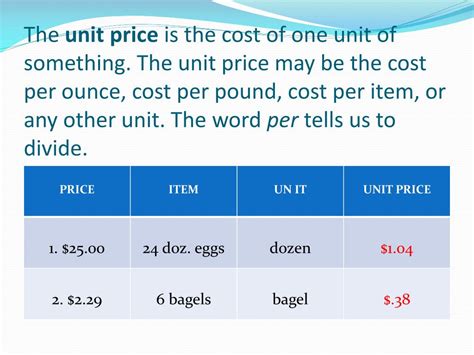
Welcome to our comprehensive guide on determining the unit cost, a critical metric in business operations and financial analysis. In this expert-driven article, we will delve into the intricacies of calculating unit costs, exploring various methodologies, real-world examples, and the practical implications of this essential concept.
Unit cost is a fundamental financial metric that quantifies the total cost associated with producing or acquiring a single unit of a good or service. It provides valuable insights into a company's operational efficiency, profitability, and overall financial health. By understanding and effectively managing unit costs, businesses can make informed decisions, optimize their operations, and gain a competitive edge in the market.
The Significance of Unit Cost

Unit cost serves as a critical tool for businesses across industries, offering a wealth of benefits and insights. Let’s explore the key reasons why unit cost analysis is indispensable:
- Profitability Analysis: Unit cost allows businesses to evaluate their profitability on a per-unit basis. By comparing the unit cost to the selling price, companies can assess their margins, identify profitable products or services, and make strategic pricing decisions.
- Cost Control: Effective unit cost management is essential for cost control. Businesses can identify areas of inefficiency, reduce waste, and optimize their production processes by analyzing unit costs. This leads to improved profitability and enhanced operational efficiency.
- Productivity Assessment: Unit cost provides a clear indication of a company's productivity. By tracking changes in unit costs over time, businesses can gauge their efficiency improvements or identify areas where productivity may be declining.
- Pricing Strategy: Understanding unit cost is crucial for developing effective pricing strategies. Companies can set competitive prices, maximize profitability, and respond to market dynamics by considering the relationship between unit cost and selling price.
- Cost-Volume-Profit Analysis: Unit cost forms the basis for cost-volume-profit (CVP) analysis, a powerful tool for evaluating the impact of changes in sales volume, costs, and prices on a company's profitability. CVP analysis helps businesses make informed decisions regarding production levels, pricing, and cost management.
- Decision-Making: Unit cost analysis plays a pivotal role in strategic decision-making. It enables businesses to evaluate the financial implications of various scenarios, such as introducing new products, expanding operations, or making investments. By considering unit costs, companies can make well-informed choices that align with their financial goals.
In the following sections, we will delve deeper into the methodologies for calculating unit costs, explore real-world examples, and discuss the practical applications of this essential financial metric.
Methodologies for Calculating Unit Cost
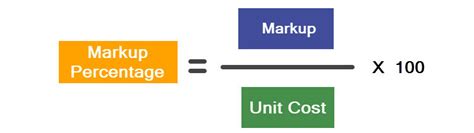
Determining unit cost involves a systematic approach that considers various factors. Here, we present three commonly used methodologies for calculating unit cost:
Method 1: Variable Costing
Variable costing, also known as direct costing, is a widely adopted methodology for calculating unit cost. It focuses on identifying and allocating variable costs to each unit of production. Variable costs are those that fluctuate directly with the level of production, such as raw materials, direct labor, and certain overhead expenses.
The formula for calculating unit cost using variable costing is as follows:
Unit Cost = (Total Variable Costs / Number of Units)
By considering only the variable costs, this methodology provides a more accurate representation of the direct costs associated with producing each unit. It helps businesses understand the true cost structure and make informed decisions regarding pricing, production levels, and cost control.
Method 2: Full Costing
Full costing, also referred to as absorption costing, takes a comprehensive approach by including both variable and fixed costs in the unit cost calculation. Fixed costs are those that remain relatively constant regardless of the level of production, such as rent, insurance, and administrative expenses.
The formula for calculating unit cost using full costing is:
Unit Cost = (Total Costs (Variable + Fixed) / Number of Units)
By incorporating fixed costs, full costing provides a more holistic view of the overall cost structure. It allows businesses to allocate fixed costs to each unit, ensuring that all expenses are considered in the unit cost calculation. This methodology is particularly useful for companies that want a complete understanding of their cost structure and profitability.
Method 3: Activity-Based Costing (ABC)
Activity-Based Costing (ABC) is a sophisticated methodology that allocates costs based on the activities or processes involved in producing a product or service. It recognizes that different activities have varying cost drivers and assigns costs accordingly.
The ABC approach involves the following steps:
- Identify Activities: Begin by identifying the specific activities or processes involved in production.
- Assign Costs to Activities: Allocate costs to each activity based on its cost drivers, such as machine hours, labor hours, or material usage.
- Assign Activity Costs to Products: Distribute the costs of each activity to the products or services based on their usage or consumption of the activity.
- Calculate Unit Cost: Determine the unit cost by summing up the allocated costs for each activity and dividing it by the number of units produced.
ABC provides a more precise allocation of costs, especially in complex production environments with multiple products or services. It helps businesses identify cost drivers, optimize resource allocation, and make informed decisions regarding product pricing and cost management.
Real-World Examples of Unit Cost Calculation
To illustrate the practical application of unit cost calculation, let’s explore two real-world examples:
Example 1: Widget Manufacturing Company
Imagine a widget manufacturing company that produces and sells widgets in various sizes and colors. The company’s production manager wants to determine the unit cost of producing a specific widget to evaluate its profitability.
Here's a breakdown of the costs incurred by the company:
Cost Category | Cost |
---|---|
Raw Materials | $2500 |
Direct Labor | $1800 |
Machine Hours | $1200 |
Overhead Expenses | $1500 |
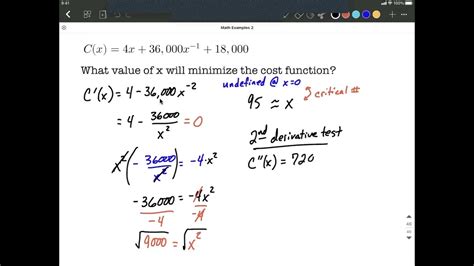
Using the variable costing methodology, the unit cost for this specific widget can be calculated as follows:
Unit Cost = (Total Variable Costs / Number of Widgets)
Assuming the company produced 1000 widgets, the unit cost would be:
Unit Cost = ($2500 + $1800 + $1200) / 1000
Unit Cost = $5500 / 1000
Unit Cost = $5.50 per widget
This calculation provides the company with valuable insights into the direct costs associated with producing each widget. By comparing this unit cost to the selling price, the company can assess its profitability and make informed decisions regarding pricing and production strategies.
Example 2: Service-Based Business
Consider a service-based business, such as a consulting firm, that provides various consulting services to its clients. The firm’s finance team wants to determine the unit cost of delivering a specific consulting service to better understand its profitability.
Here's a breakdown of the costs associated with providing this consulting service:
Cost Category | Cost |
---|---|
Consultant Salaries | $20,000 |
Office Rent | $5,000 |
Marketing Expenses | $3,000 |
Administrative Overhead | $2,000 |
Using the full costing methodology, the unit cost for delivering this specific consulting service can be calculated as follows:
Unit Cost = (Total Costs (Variable + Fixed) / Number of Services)
Assuming the firm provided this service to 50 clients, the unit cost would be:
Unit Cost = ($20,000 + $5,000 + $3,000 + $2,000) / 50
Unit Cost = $30,000 / 50
Unit Cost = $600 per service
This calculation provides the consulting firm with a comprehensive understanding of the total costs associated with delivering each consulting service. By comparing this unit cost to the revenue generated from each service, the firm can assess its profitability and make strategic decisions regarding resource allocation and pricing.
Practical Applications and Future Implications
Unit cost analysis has far-reaching practical applications across various industries and business functions. Let’s explore some of the key areas where unit cost plays a vital role:
Pricing Strategy
Understanding unit cost is crucial for developing effective pricing strategies. Businesses can set competitive prices, maximize profitability, and respond to market dynamics by analyzing unit costs. By comparing unit cost to market prices, companies can identify opportunities for value-based pricing or cost-plus pricing strategies.
Cost Management and Optimization
Unit cost analysis provides a powerful tool for cost management and optimization. By identifying areas of high unit cost, businesses can implement cost-cutting measures, improve efficiency, and enhance their overall cost structure. This enables companies to stay competitive, increase profitability, and maintain a sustainable business model.
Product Mix Decisions
Unit cost analysis helps businesses evaluate the profitability of different products or services within their portfolio. By comparing unit costs across various offerings, companies can make informed decisions regarding product mix, focusing on the most profitable products or services. This strategic approach allows businesses to optimize their resources and maximize overall profitability.
Performance Evaluation
Unit cost serves as a key performance indicator (KPI) for businesses. By tracking changes in unit costs over time, companies can assess their operational efficiency, productivity, and cost control efforts. This enables them to identify areas for improvement, implement process enhancements, and continuously strive for operational excellence.
Future Implications
As businesses continue to evolve and face increasing competition, unit cost analysis will remain a critical component of strategic decision-making. With advancements in technology and data analytics, companies will have access to more sophisticated tools and methodologies for calculating and analyzing unit costs. This will enable them to make data-driven decisions, optimize their operations, and gain a competitive edge in the market.
Furthermore, as businesses embrace digital transformation and adopt innovative technologies, unit cost analysis will play a crucial role in evaluating the financial implications of these initiatives. By understanding the unit costs associated with digital transformation projects, companies can make informed choices, allocate resources effectively, and ensure the success and profitability of their digital endeavors.
Conclusion

In conclusion, unit cost is a vital metric for businesses seeking to optimize their operations, improve profitability, and make strategic decisions. By adopting the appropriate methodologies, such as variable costing, full costing, or activity-based costing, businesses can gain valuable insights into their cost structure and make informed choices.
Unit cost analysis enables companies to assess their profitability, control costs, optimize their product mix, and evaluate performance. As businesses navigate an ever-changing landscape, unit cost will continue to be a powerful tool for financial analysis and strategic planning. By embracing advanced analytics and leveraging technology, businesses can unlock the full potential of unit cost analysis and drive their success in a competitive market.
How often should unit cost be calculated and reviewed?
+The frequency of calculating and reviewing unit cost depends on the nature of the business and its operational environment. In general, it is recommended to calculate unit cost at regular intervals, such as monthly or quarterly, to capture any changes in costs and production levels. However, in dynamic industries with frequent fluctuations, more frequent calculations may be necessary. Additionally, businesses should review unit cost whenever there are significant changes in production processes, cost structures, or market conditions that may impact profitability.
What are some common challenges in calculating unit cost accurately?
+Calculating unit cost accurately can present several challenges. One common challenge is allocating overhead costs accurately, especially in complex production environments. Overhead costs can be challenging to allocate to specific units, requiring careful analysis and appropriate allocation methods. Additionally, identifying and differentiating between variable and fixed costs can be tricky, especially for costs that exhibit mixed behavior. Another challenge lies in capturing all relevant costs, including indirect costs, to ensure a comprehensive unit cost calculation.
How can businesses use unit cost analysis to improve their profitability?
+Unit cost analysis provides businesses with valuable insights to improve profitability. By comparing unit cost to selling price, businesses can identify products or services with high margins and focus on optimizing their production or delivery. Unit cost analysis also helps identify areas of cost inefficiency, allowing businesses to implement cost-saving measures and improve overall profitability. Additionally, by analyzing unit cost trends over time, businesses can make informed decisions regarding pricing strategies, cost management initiatives, and resource allocation to maximize profitability.